Innovation Village, Gateshead - An Overview
As the construction industry drives to meet the Government’s 2025 Future Homes standard, we are very proud to be involved with Innovation Village, Gateshead. The project set out to give the sector great confidence in utilising modern methods at scale, coupled with the testing of sustainable energy solutions to test the energy performance and inform the eco strategy for future housing developments. We are very pleased to say that the proposal was awarded the prestigious Constructing Excellence’ National Award for Innovation for 2021.
IDP collaborated closely with Home Group and Engie to develop the proposals of 41 houses which were completed in 2019 as a live test site. The scheme tests five different MMC methods alongside traditional building techniques which were used as a control for testing:
ilke Homes (volumetric light steel frame)
Premier (volumetric light steel frame)
Xella (aerated concreted panelised system)
Intelligent Steel (panelised light steel frame)
Simply Modular (volumetric timber frame
The way in which the homes are constructed, heated, hot water, lighting, ventilation, home appliances and cooking all contribute to the amount of carbon dioxide created. MMC, as well as better heating systems, insulation and renewable energy have already reduced the levels of carbon dioxide produced. Building the development in this manner has enabled the development to already comply with the Governments 2025 Future Homes Standard.
The construction of houses in a factory environment drives a reduction in waste, minimises deliveries to site during the construction phase and analysis has proven that embodied carbon within modular housing is less than their traditionally built counterparts. Higher levels of quality control in the factories also reduced snagging, accelerated the build programme by faster installation on site and minimised disruption to surrounding residents and stakeholders.
Environmental impact was a fundamental consideration for the project. The measures considered, and the positive impact these would have, included ground source heat pumps, PV panels, sustainable drainage systems, reducing fuel poverty for customers, reduction in waste, off-site manufacturing, standardisation of components and partnership working.
Not only has the development provided a test bed for MMC and sustainable technologies, the proposals have created a desirable community that dispels the myths around modular housing. The aesthetically pleasing development showcases the way in which houses can be constructed today; and that MMC and traditional construction can visually stand side by side.
We believe that the drive towards carbon neutral housing is taking pace and MMC will become even more prominent in the sector. The technical knowledge gained from delivering this scheme and the comparative data on the competing construction methods within the development will determine a wide social benefit for future house building.
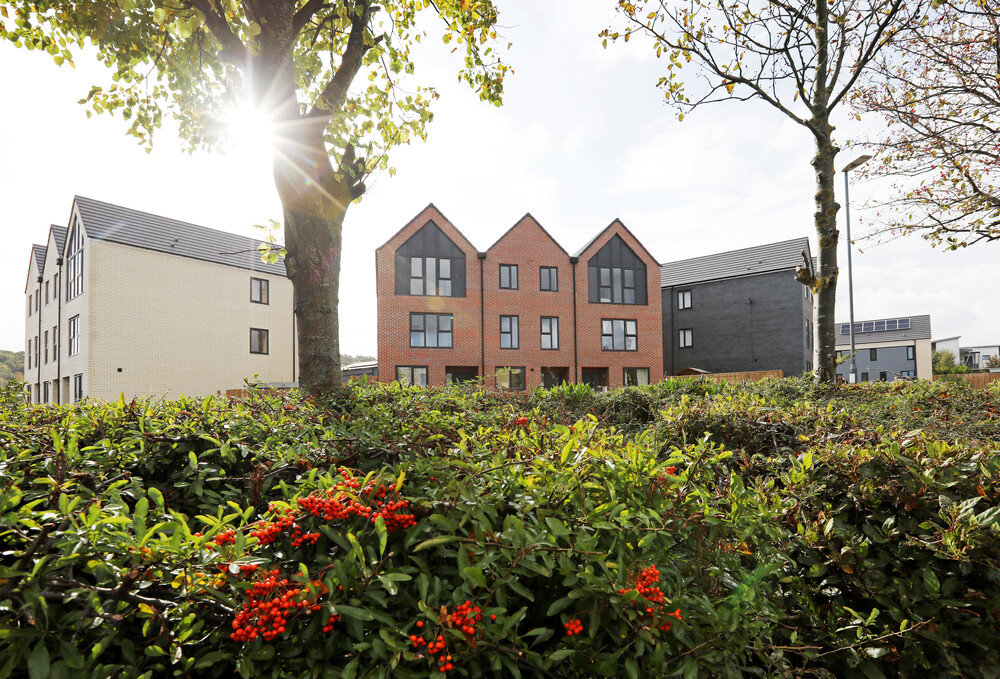
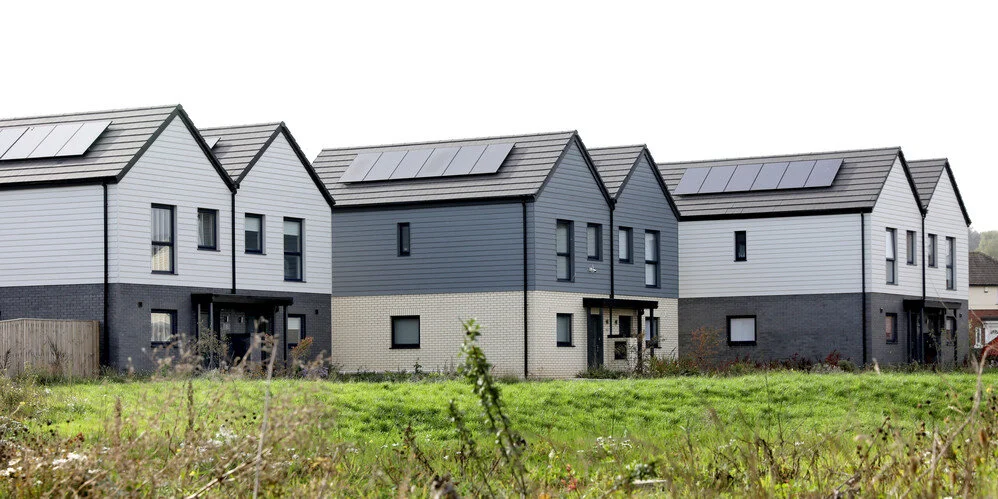
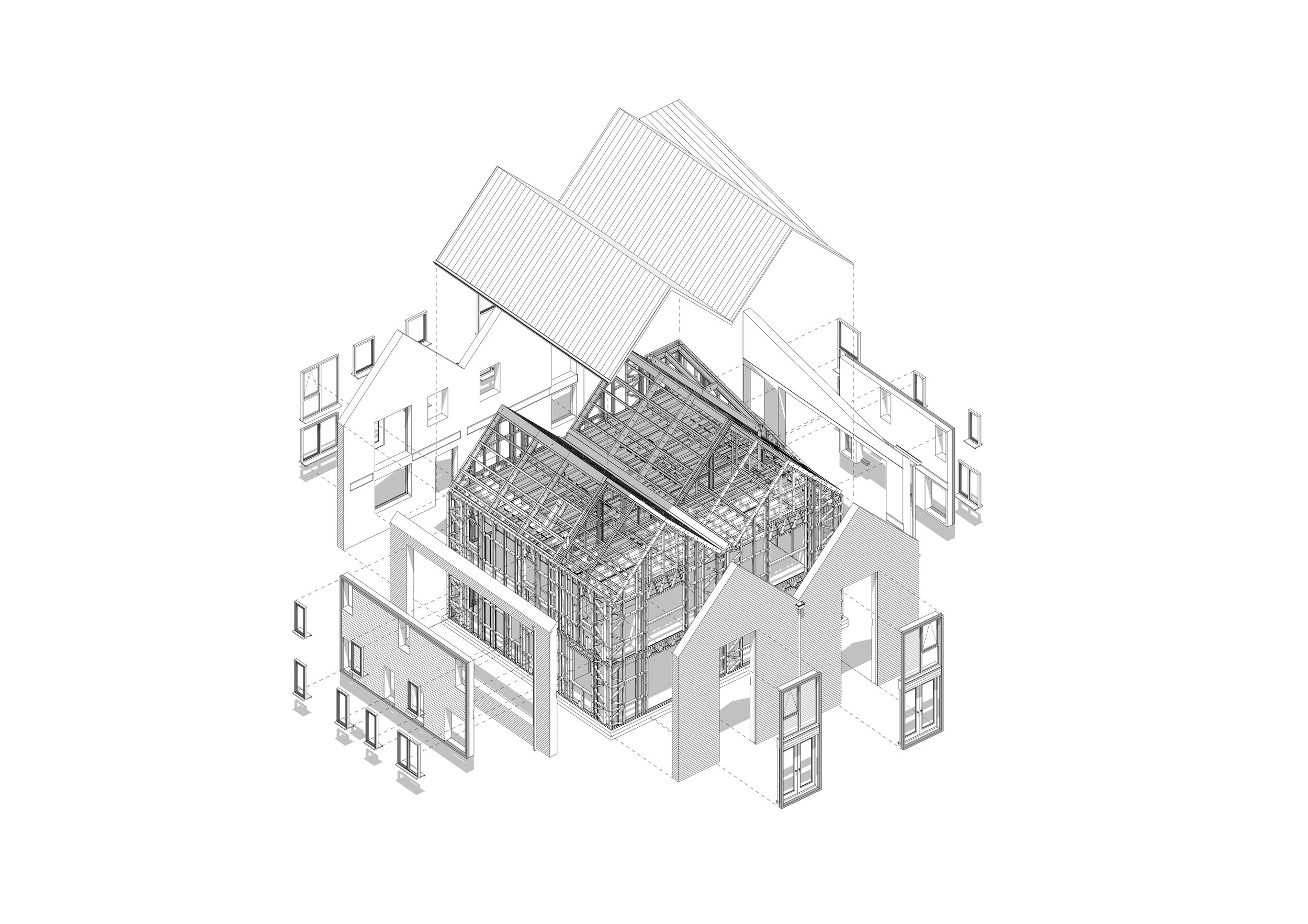
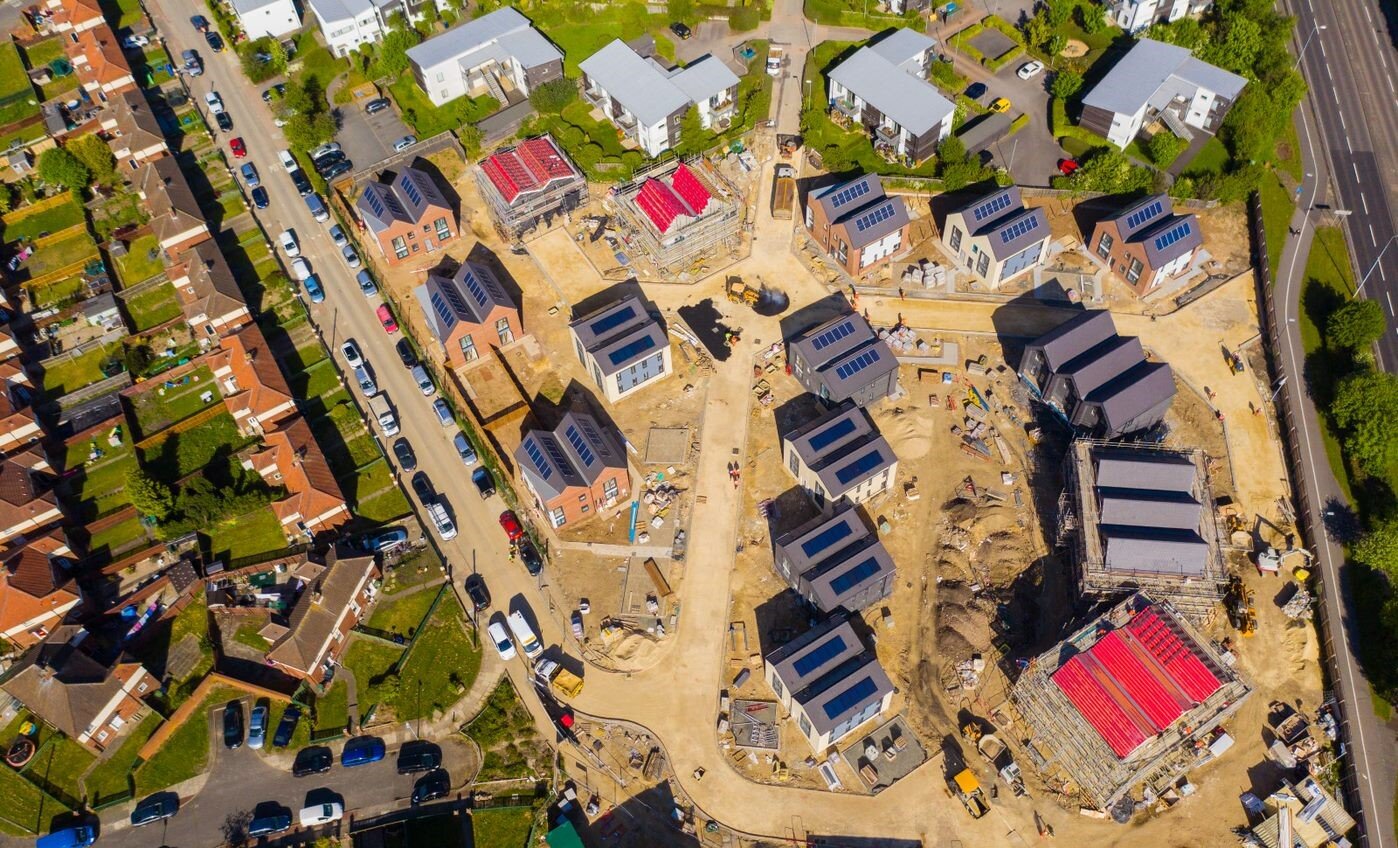
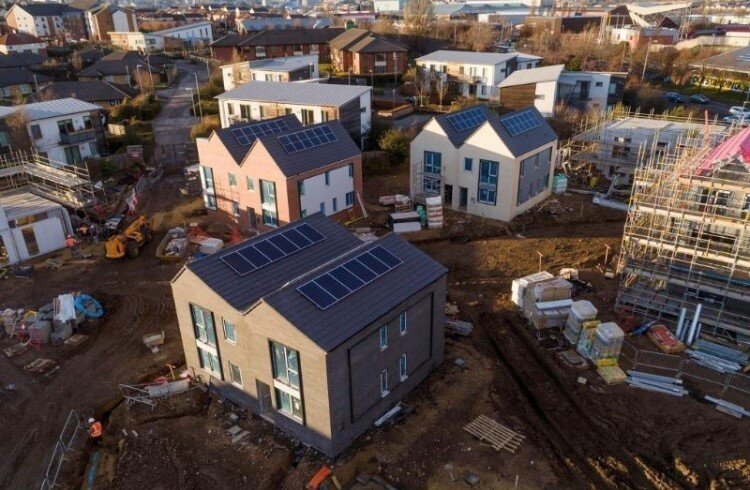
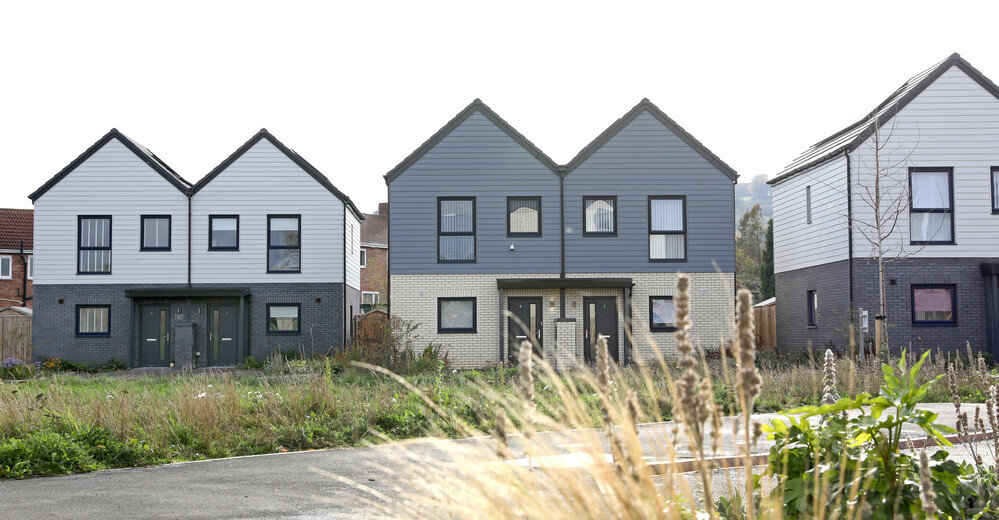
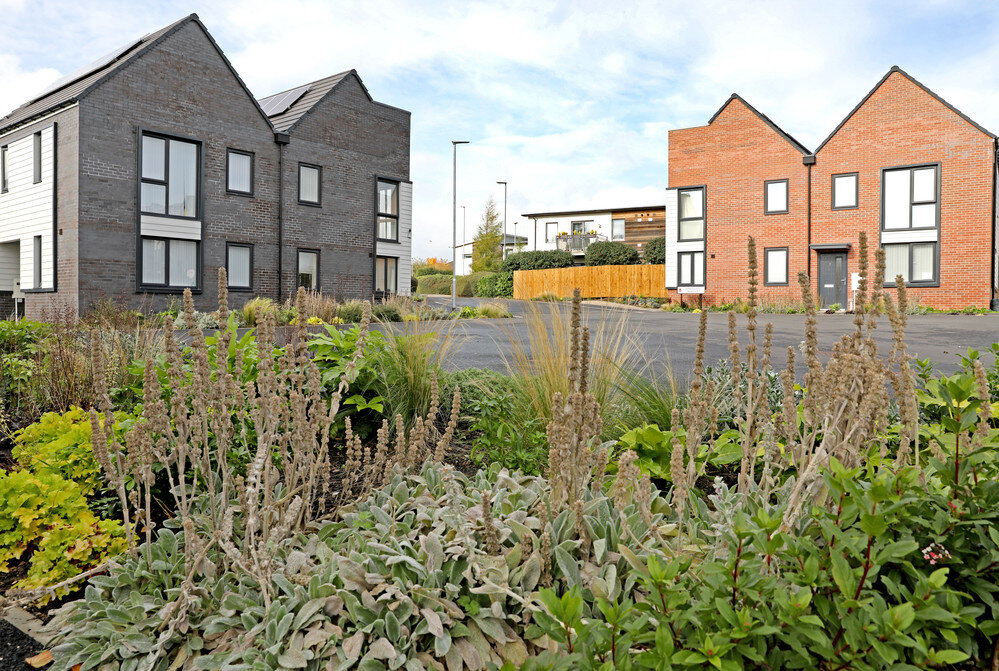
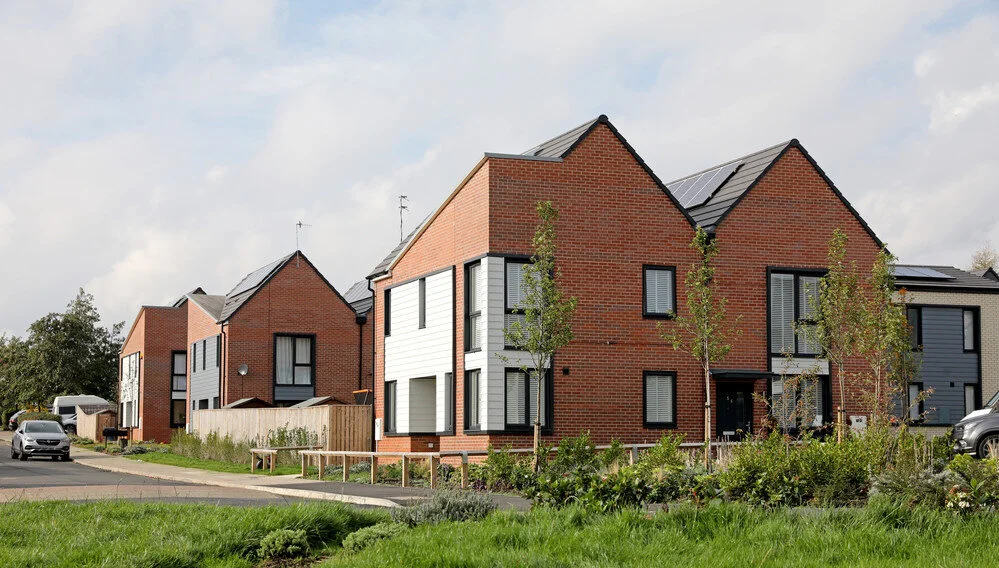
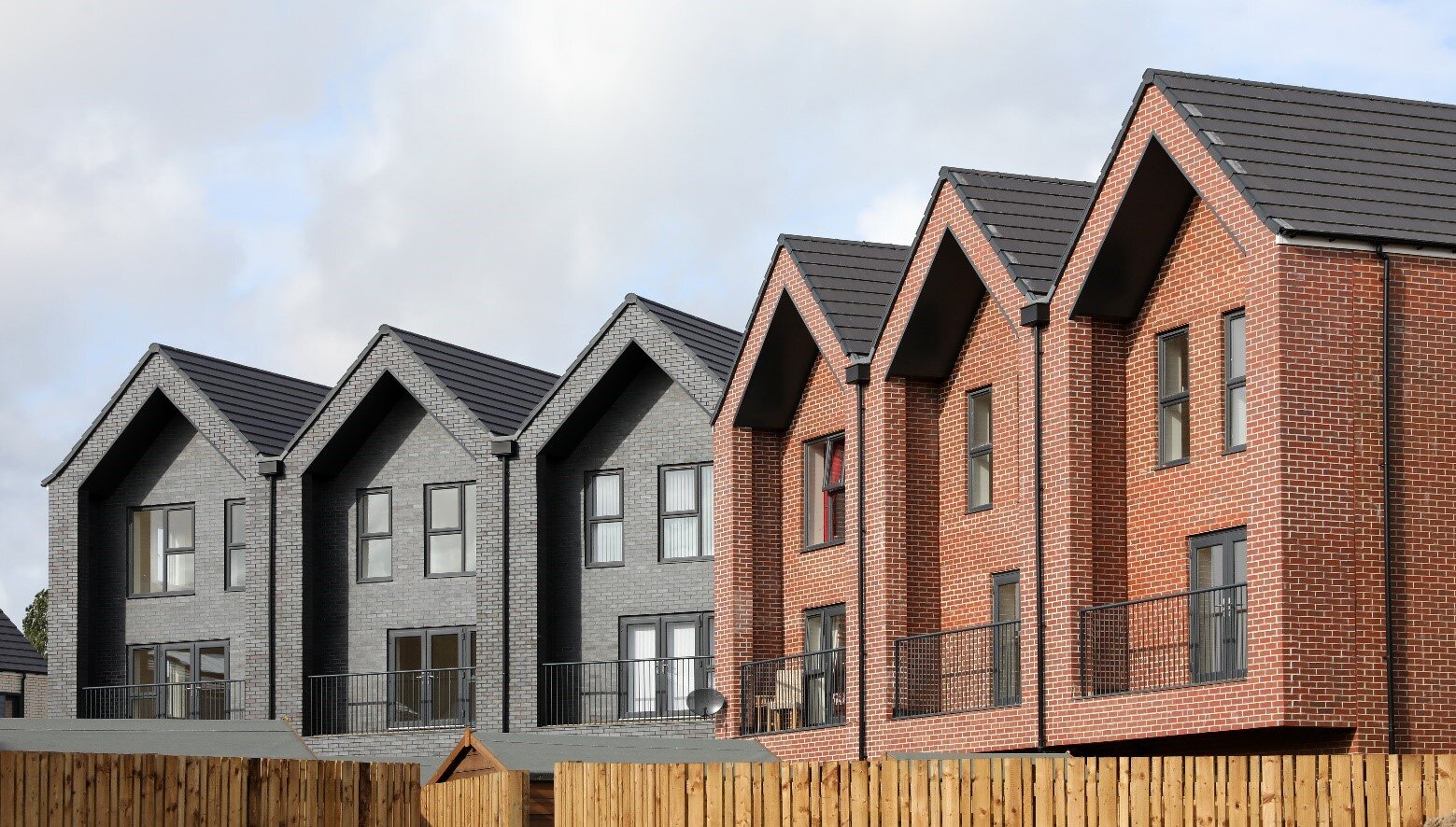
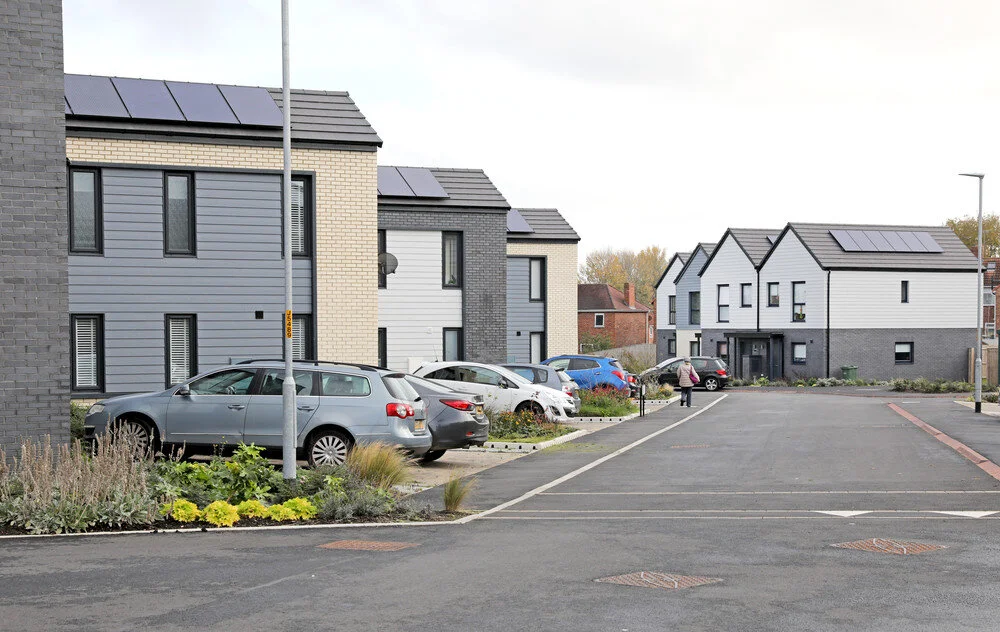
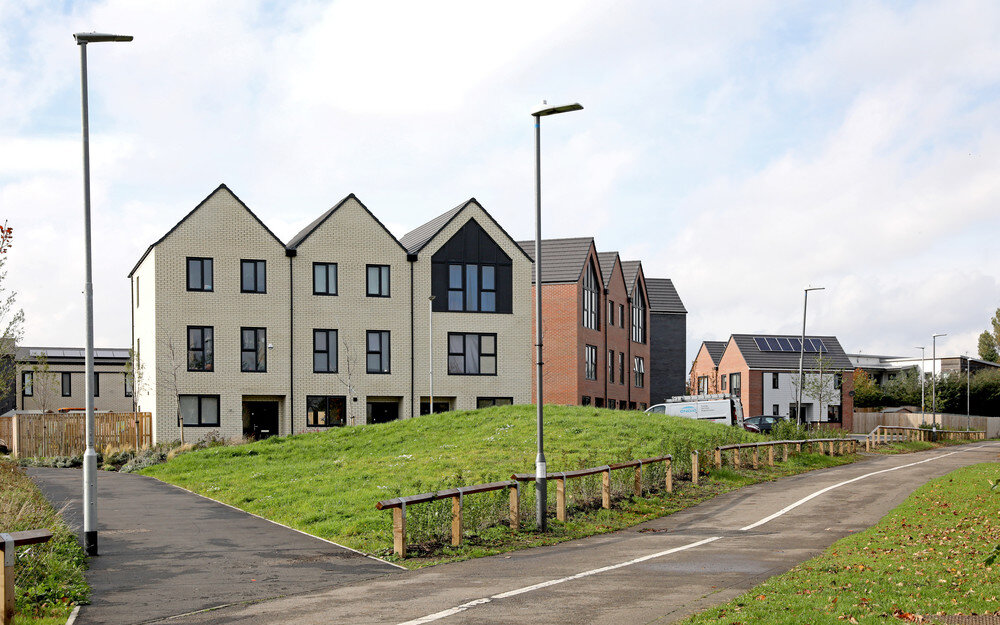
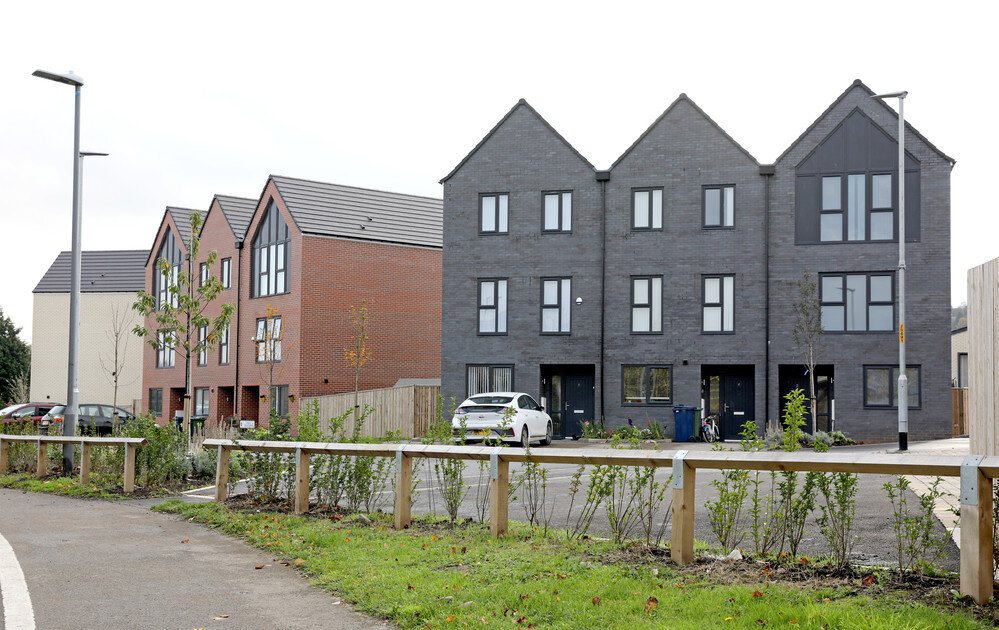